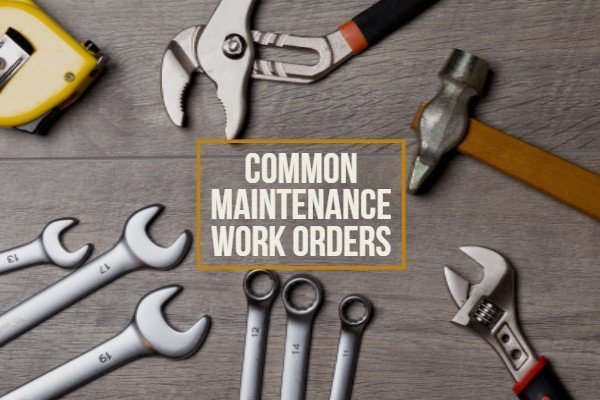
What’s an essential skill for a successful fleet management career? Maintenance expertise is an example. One of the biggest fleet management tasks is reducing downtime by finding out how to manage equipment asset maintenance.
Where’s the proof? Try searching “fleet manager” on job boards. On 9 out of 10 jobs, you will find a qualification along the lines of “manage equipment assets and their maintenance schedule”. In fact, it’s often one of the first listed items under the job duties.
This article is dedicated towards the basics of how to manage equipment asset. We will cover basic best practices, discuss facilitating these practices with work orders, and share common work orders.
Basics of Equipment Asset Maintenance
Every fleet needs a maintenance program. After all, fleets are useless if its vehicles are off the road! A competent maintenance program, therefore, reduces downtime and improves productivity.
Some best practices for fleet managers to master include:
#1: Creating Policies
Firstly, every fleet manager needs to know how to create inspection and maintenance policies. Policies capture everything in the maintenance cycle including purchasing new vehicles, managing daily check ups, and scheduling maintenance jobs.
#2: Managing Policies
Secondly, every fleet manager needs to know how to manage equipment asset policies. In other words, are people listening to what you are telling them to do? Managers are responsible for training staff, overseeing their work, and tweaking & improving policies.
Using Work Orders to Manage Maintenance
After understanding the above 2 principles, the next challenge is translating policies into real-world success. This is where work orders comes handy. Why?
Work orders and maintenance policies go hand-in-hand because work orders organize employees to follow maintenance policies.
Here are three common work orders.
First Example: Regular Checkups
A common maintenance policy is creating regular checkups such as oil changes or tire checks. That being said, fleet managers commonly have an issue with employees forgetting or missing routine jobs. In turn, missed jobs leads to downtime.
As a result, fleet managers rely on assigning periodic work orders. For instance, a manager might create a monthly work order for checking lights. This allows managers to 1) remind employees that they are responsible for regular tasks, and 2) review jobs to confirm their completion.
Second Example: Driver – Mechanic Communication
Another common work order are driver/mechanic jobs. Who are the biggest vehicle users? Drivers, of course! Drivers are often the first people to notice vehicle issues. Consequently, fleet managers need a way for drivers to assign jobs to mechanics.
Work orders provide a bridge between drivers and mechanics. For example, a lot of fleets use online CCMS. Online CMMS allow drivers to complete check ups on their phone and assign work orders to mechanics if there are any vehicle faults.
Third Example: Proactive Maintenance
Finally, it’s worth discussing preventative maintenance. Preventative maintenance is a best practice when it comes to how to manage equipment asset. In simple words, proactive maintenance means preventing downtime by fixing small problems.
A modern preventative maintenance work order involves:
- Using telematics to collect vehicle data such as engine faults, fuel mileage, and voltage.
- Creating “danger readings”. For example, some companies use high voltage as an indicator for vehicle check-ups.
- Using software to automatically create work orders when a vehicle goes into a danger reading.
Click here to read another article about CMMS & Preventative Maintenance.